Your Total Handbook to Preventing Weld Undercut Like a Pro
Wiki Article
Mastering the Art of Welding: Just How to Avoid Undercut Welding Issues for Flawless Manufacture Outcomes
By understanding the origin causes of undercut welding and carrying out effective methods to avoid it, welders can boost their craft to new levels of excellence. In the search of perfect manufacture results, understanding the art of welding to stay clear of undercut concerns is not just a skill but a necessity for those striving for excellence in their job.Understanding Undercut Welding

To prevent undercut welding, welders ought to ensure correct welding specifications, such as adjusting the current, voltage, travel speed, and maintaining the proper electrode angle. By understanding the reasons of undercut welding and applying precautionary measures, welders can achieve premium, structurally sound welds.
Root Causes Of Undercut in Welding
Comprehending the factors that add to undercut in welding is necessary for welders to generate top notch, structurally audio welds. Poor welding wrong or present welding rate can additionally contribute to undercut. Understanding these causes and implementing proper welding techniques can aid prevent damaging concerns, ensuring solid and sturdy welds.Techniques to stop Undercutting

To reduce the danger of damaging in welding, welders can use tactical welding methods aimed at enhancing the high quality and integrity of the weld joints. In addition, utilizing the correct welding method for the certain joint arrangement, such as weave or stringer beads, can contribute to minimizing damaging.
Additionally, proper joint prep work, including making sure tidy base materials devoid of contaminants and using the appropriate welding consumables, is critical in avoiding undercut issues. Using back-step welding strategies and managing the weld bead account can additionally aid disperse heat evenly and decrease the threat of undercut. Normal inspection of the weld joint throughout like it and after find out here now welding, along with executing high quality guarantee steps, can assist in dealing with and detecting damaging problems without delay. By implementing these techniques diligently, welders can achieve flawless fabrication results with marginal undercut defects.
Significance of Correct Welding Parameters
Selecting and keeping appropriate welding parameters is crucial for achieving successful welds with very little flaws. Welding specifications describe variables such as voltage, current, take a trip speed, electrode angle, and protecting gas flow price that straight influence the welding process. These specifications should be carefully readjusted based on the type of product being welded, its density, and the welding technique utilized.Correct welding specifications ensure the appropriate quantity of heat is put on melt the base metals and filler material evenly. If the specifications are established as well high, it can lead to too much warmth input, creating distortion, burn-through, or spatter. On the other hand, if the criteria are too low, insufficient fusion, absence of penetration, or undercutting might occur.
Top Quality Assurance in Welding Workflow
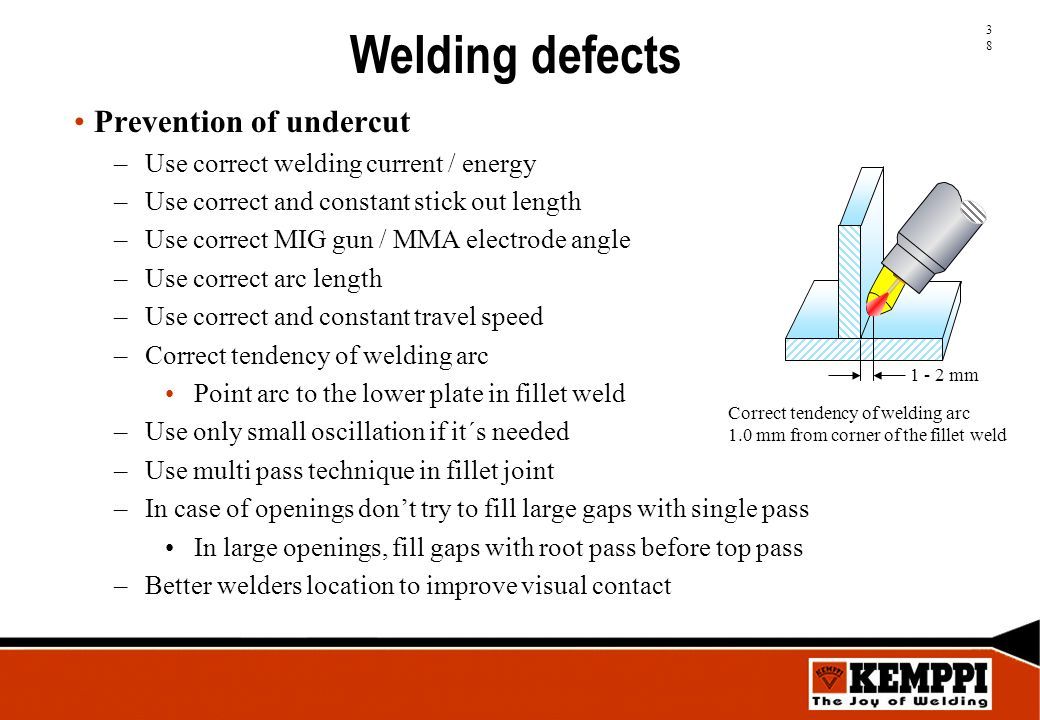
Final Thought
Finally, grasping the art of welding needs a thorough understanding of undercut welding, its reasons, and techniques to prevent it. By ensuring proper welding criteria and implementing quality control practices, flawless manufacture outcomes can be accomplished. It is essential for welders to constantly aim for quality in their welding procedures to stay clear of undercut concerns and generate premium welds.Undercut welding, a typical problem in Find Out More welding procedures, happens when the weld steel doesn't appropriately load the groove and leaves a groove or clinical depression along the bonded joint.To stop undercut welding, welders must make sure proper welding parameters, such as readjusting the present, voltage, traveling rate, and maintaining the proper electrode angle. Poor welding present or incorrect welding speed can additionally add to undercut.To reduce the risk of undercutting in welding, welders can utilize critical welding strategies aimed at improving the quality and stability of the weld joints.In verdict, grasping the art of welding calls for a detailed understanding of undercut welding, its causes, and techniques to prevent it.
Report this wiki page